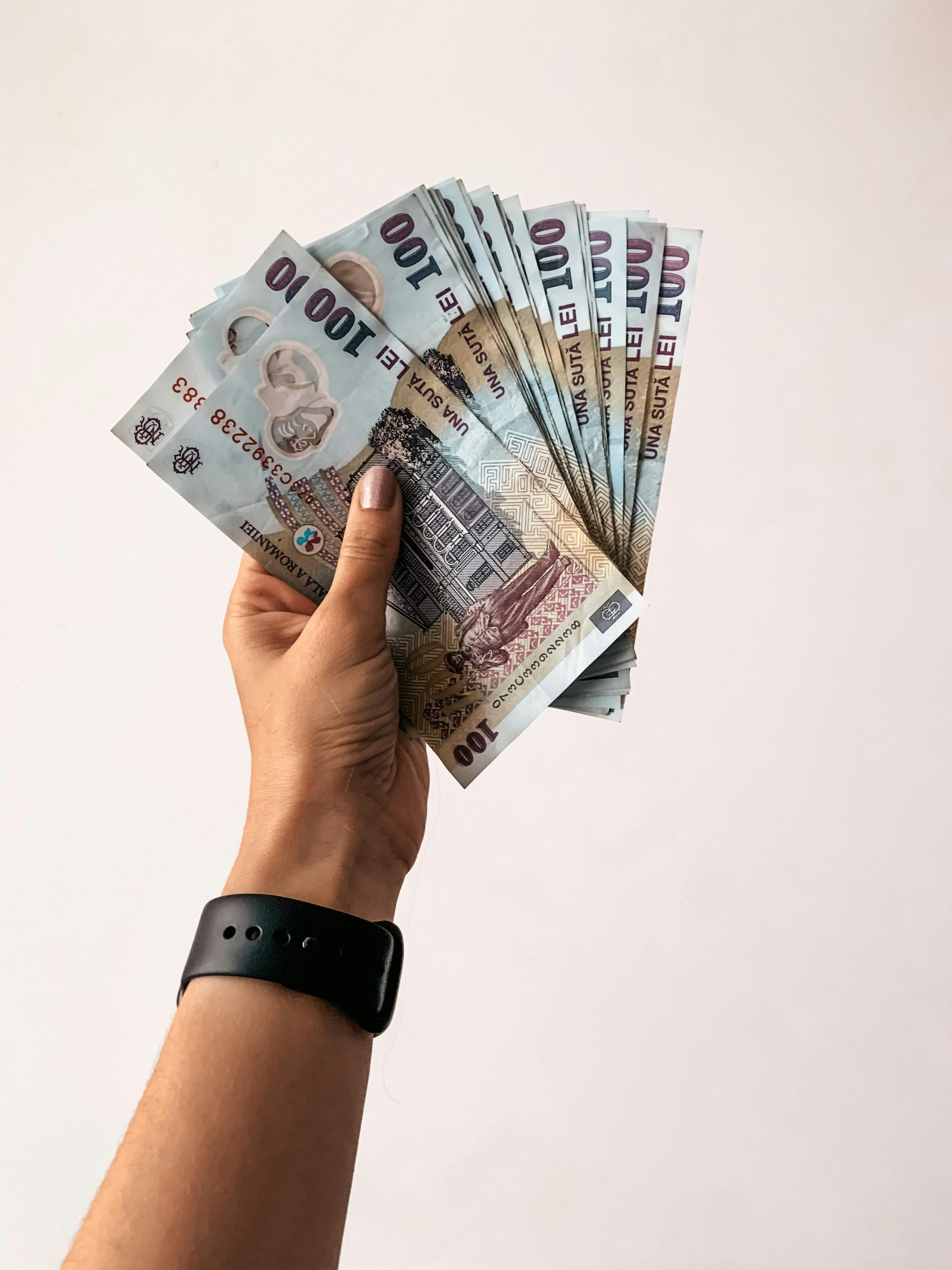
Material handling equipment (MHE) is the backbone of numerous industries, facilitating the efficient movement, storage, control, and protection of materials throughout the supply chain. From manufacturing and warehousing to logistics and construction, MHE plays a critical role in optimizing operations, reducing costs, and ensuring timely delivery of goods. Selecting the right MHE is a significant decision that directly impacts a company’s productivity, safety, and profitability.
However, one of the most pressing challenges businesses face when investing in MHE is balancing cost and quality. While it’s tempting to opt for the cheapest options available, compromising on quality can lead to increased maintenance expenses, frequent breakdowns, safety hazards, and reduced operational efficiency in the long run. Conversely, investing in top-of-the-line equipment can strain budgets and limit financial flexibility. Finding the right balance between cost and quality is essential for maximizing return on investment and achieving sustainable growth.
This overview posits that it is possible to invest in superior material handling equipment without breaking the bank. This can be achieved by employing strategic planning, exploring alternative acquisition methods, and prioritizing essential features. By taking a holistic approach to MHE investment, businesses can secure reliable, high-performing equipment while staying within their budgetary constraints.
Understanding the True Cost of Ownership
When evaluating material handling equipment (MHE), it’s crucial to look beyond the initial purchase price and consider the total cost of ownership (TCO). The TCO encompasses all expenses associated with owning and operating MHE throughout its lifespan, providing a more comprehensive view of the investment’s financial impact.
Several factors contribute to the TCO of MHE. These include:
- Maintenance: Regular servicing, inspections, and replacement of worn parts.
- Repairs: Unforeseen breakdowns and the associated costs of labor and parts.
- Energy Consumption: The electricity, fuel, or other energy sources required to operate the equipment.
- Downtime: Lost productivity due to equipment failures and maintenance activities.
- Lifespan: The expected duration of the equipment’s operational life before it needs to be replaced.
A common mistake is to prioritize low-cost, low-quality equipment based solely on its lower upfront price tag. However, these options often incur higher maintenance costs, require more frequent repairs, consume more energy, and have shorter lifespans. The cumulative effect of these factors can significantly increase the TCO, making the “cheaper” option ultimately more expensive in the long run.
In contrast, higher-quality, more durable MHE may have a higher initial price but typically boasts lower maintenance requirements, fewer breakdowns, better energy efficiency, and a longer lifespan. This can translate to substantial long-term savings, as the reduced operating costs and extended service life offset the higher upfront investment. Therefore, a comprehensive understanding of the TCO is essential for making informed decisions and maximizing the return on investment in MHE.
Strategic Planning and Needs Assessment
Before investing in material handling equipment (MHE), conducting a thorough needs assessment is of paramount importance. This involves a systematic evaluation of current and future operational requirements to ensure that the selected equipment aligns with the specific needs of the business. A well-executed needs assessment minimizes the risk of overspending on unnecessary features or underinvesting in equipment that is inadequate for the task.
The needs assessment should identify specific operational requirements, including:
- Material Types: The types of materials to be handled (e.g., pallets, boxes, bulk materials) and their physical characteristics (e.g., weight, dimensions, fragility).
- Handling Volumes: The quantity of materials to be moved within a given timeframe (e.g., per hour, per day).
- Operational Environment: The characteristics of the work environment (e.g., indoor/outdoor, temperature, space constraints).
- Workflow Patterns: The flow of materials through the facility and the distances they need to be transported.
Based on the needs assessment, businesses should prioritize essential features and avoid unnecessary add-ons. This involves distinguishing between “must-have” features that directly impact performance and safety and “nice-to-have” features that offer marginal benefits. By focusing on core functionality, companies can optimize their investment and avoid paying for features they don’t need.
Ultimately, the goal is to develop a long-term material handling strategy that is aligned with the overall business goals. This strategy should outline how MHE will be used to support operational efficiency, reduce costs, improve safety, and enhance customer satisfaction. By integrating material handling into the broader business strategy, companies can ensure that their MHE investments contribute to sustainable growth and competitive advantage.
Exploring Alternative Acquisition Methods
Acquiring material handling equipment (MHE) doesn’t always necessitate a direct purchase. Exploring alternative acquisition methods can significantly impact your budget and offer greater flexibility.
Leasing vs. Buying:
Leasing MHE involves making periodic payments for the use of the equipment over a specified term, while buying entails outright ownership. Each option has its own set of pros and cons:
- Leasing:
- Pros: Lower upfront costs, predictable monthly payments, potential tax benefits, flexibility to upgrade equipment, and often includes maintenance services.
- Cons: Higher overall cost compared to buying, no asset ownership, potential limitations on usage.
- Financial Implications: Impacts cash flow positively in the short-term but can be more expensive long-term.
- Flexibility: Allows for easy upgrades to newer models as technology evolves.
- Maintenance Responsibilities: Often handled by the leasing company.
- Buying:
- Pros: Asset ownership, long-term cost savings, greater control over usage, and potential resale value.
- Cons: Higher upfront costs, responsibility for maintenance and repairs, and potential for equipment obsolescence.
- Financial Implications: Requires significant capital investment upfront but can be more cost-effective long-term.
- Flexibility: Requires selling the asset to upgrade or change equipment.
- Maintenance Responsibilities: Falls on the owner.
Purchasing Used or Refurbished Equipment:
Purchasing used or refurbished MHE can be a cost-effective alternative to buying new, but it’s crucial to assess the risks and benefits carefully:
- Benefits: Significantly lower purchase price, immediate availability.
- Risks: Potential for hidden defects, limited warranty, shorter lifespan, and higher maintenance costs.
- Tips for Evaluating:
- Thoroughly inspect the equipment for signs of wear and tear.
- Request maintenance records and service history.
- Obtain a professional inspection from a qualified technician.
- Negotiate a reasonable warranty period.
- Verify the reliability and reputation of the seller.
Financing Options:
If purchasing MHE is the preferred option, exploring financing solutions can help manage the upfront costs:
- Loans: Secured or unsecured loans from banks or credit unions.
- Lines of Credit: Revolving credit accounts that provide access to funds as needed.
- Equipment Financing: Specialized loans specifically designed for purchasing equipment, often offered by equipment manufacturers or leasing companies.
By carefully evaluating these alternative acquisition methods, businesses can find the most cost-effective way to obtain the MHE they need without straining their financial resources.
Prioritizing Essential Features and Quality Components
When investing in material handling equipment (MHE), it’s essential to prioritize features that directly impact performance and safety. These critical features are the foundation of efficient and reliable operations, ensuring that the equipment meets the specific needs of the business and protects its employees.
Some of the most important features to consider include:
- Load Capacity: The maximum weight that the equipment can safely lift or transport.
- Durability: The ability of the equipment to withstand wear and tear, harsh environments, and heavy use.
- Ergonomics: The design of the equipment to minimize strain and fatigue on operators, promoting comfort and productivity.
- Safety Features: Built-in mechanisms and technologies that prevent accidents, such as emergency stops, warning systems, and load sensors.
- Reliability: The consistency and dependability of the equipment’s performance over time.
Focusing on reputable manufacturers and suppliers with proven track records is crucial for ensuring that the MHE meets these standards. Established manufacturers typically have rigorous quality control processes, use high-grade materials, and offer comprehensive warranties. They are also more likely to provide ongoing support and service throughout the equipment’s lifespan.
Investing in high-quality components is essential for contributing to the longevity of the equipment. Opting for premium engines, hydraulics, electrical systems, and other critical components can significantly extend the service life of the MHE and reduce the need for frequent repairs. While these components may have a higher initial cost, they offer long-term value by minimizing downtime, improving performance, and enhancing overall reliability. By prioritizing essential features and quality components, businesses can make informed decisions that optimize their MHE investments and ensure long-term operational success.
Preventive Maintenance and Training Programs
Preventive maintenance and comprehensive training programs are crucial for maximizing the lifespan and effectiveness of material handling equipment (MHE). Neglecting these aspects can lead to increased downtime, higher repair costs, and a greater risk of accidents, ultimately undermining the value of the initial investment.
Preventive maintenance plays a vital role in extending the lifespan of MHE. By implementing a proactive maintenance schedule, businesses can identify and address potential problems before they escalate into major breakdowns. This includes:
- Regular Inspections: Conducting routine inspections to identify signs of wear and tear, damage, or malfunction.
- Lubrication: Ensuring that all moving parts are properly lubricated to reduce friction and prevent premature wear.
- Timely Repairs: Addressing minor issues promptly to prevent them from developing into more significant problems.
In addition to preventive maintenance, proper training for operators and maintenance personnel is essential. Well-trained operators are more likely to use the equipment safely and efficiently, reducing the risk of accidents and minimizing wear and tear. Trained maintenance personnel are better equipped to diagnose and repair problems quickly, minimizing downtime and keeping the equipment in optimal condition. The benefits of proper training include:
- Reduced Risk of Accidents: Trained operators are more aware of safety procedures and are better equipped to handle potential hazards.
- Improved Efficiency: Skilled operators can maximize the equipment’s performance, increasing productivity and reducing cycle times.
- Minimized Downtime: Trained maintenance personnel can quickly identify and resolve problems, minimizing disruptions to operations.
By investing in preventive maintenance and comprehensive training programs, businesses can protect their MHE investments, improve operational efficiency, and create a safer work environment.
Case Studies: Success Stories of Cost-Effective MHE Investments
Examining real-world examples of companies that have successfully balanced cost and quality in their material handling equipment (MHE) investments provides valuable insights and practical guidance. These case studies highlight specific strategies employed and the positive outcomes achieved.
- Kemper Equipment: Kemper provided a cost-effective wash plant by prioritizing production and portability. They developed a system that could move quickly and easily and function within the operation’s existing space. Additionally, they designed and manufactured a chute system that decreased waste from 11% to 3% for a customer dealing with a chute producing too much waste. Another customer was dealing with a scale that wouldn’t calibrate correctly, and Kemper improved the accuracy of an 1800-2200 TPH Railcar Loadout, which led to upset customers.
- Materials Handling Systems, Inc: Regal Granite & Marble selected top raw materials providers, chose his location carefully, and researched his equipment purchases. A wire company experiencing a drag in productivity and risking injury in its “bunching” application increased productivity with a Gorbel workstation crane.
- MasterMover: A global transformer manufacturer streamlined heavy transformer movement at its Mexico City factory with MasterMover electric tug solution. Terex Omagh implemented forklift-free processes in their Materials Processing division, driving safer and more efficient operations with remote controlled electric tugs.
- Hyster: Businesses that carefully align their forklift power source to their operational requirements arrive at the strongest outcomes.
These case studies demonstrate that by carefully considering their specific needs, exploring alternative acquisition methods, and prioritizing essential features, companies can achieve a favorable balance between cost and quality in their MHE investments, leading to improved efficiency, reduced costs, and enhanced safety.
Conclusion
In conclusion, it is indeed possible to invest in superior material handling equipment (MHE) without incurring excessive costs. By adopting a strategic approach and carefully considering the various factors involved, businesses can achieve a favorable balance between cost and quality, optimizing their operations without breaking the bank.
The key strategies for balancing cost and quality in MHE investments include:
- Understanding the true cost of ownership beyond the initial purchase price.
- Conducting a thorough needs assessment to identify specific operational requirements.
- Prioritizing essential features and avoiding unnecessary add-ons.
- Exploring alternative acquisition methods such as leasing or purchasing used equipment.
- Focusing on reputable manufacturers and suppliers with proven track records.
- Investing in preventive maintenance and comprehensive training programs.
With careful planning, strategic acquisition methods, and a focus on essential features and quality components, businesses can optimize their material handling operations, enhance efficiency, improve safety, and reduce costs. By embracing these principles, companies can ensure that their MHE investments contribute to long-term success and a sustainable competitive advantage.