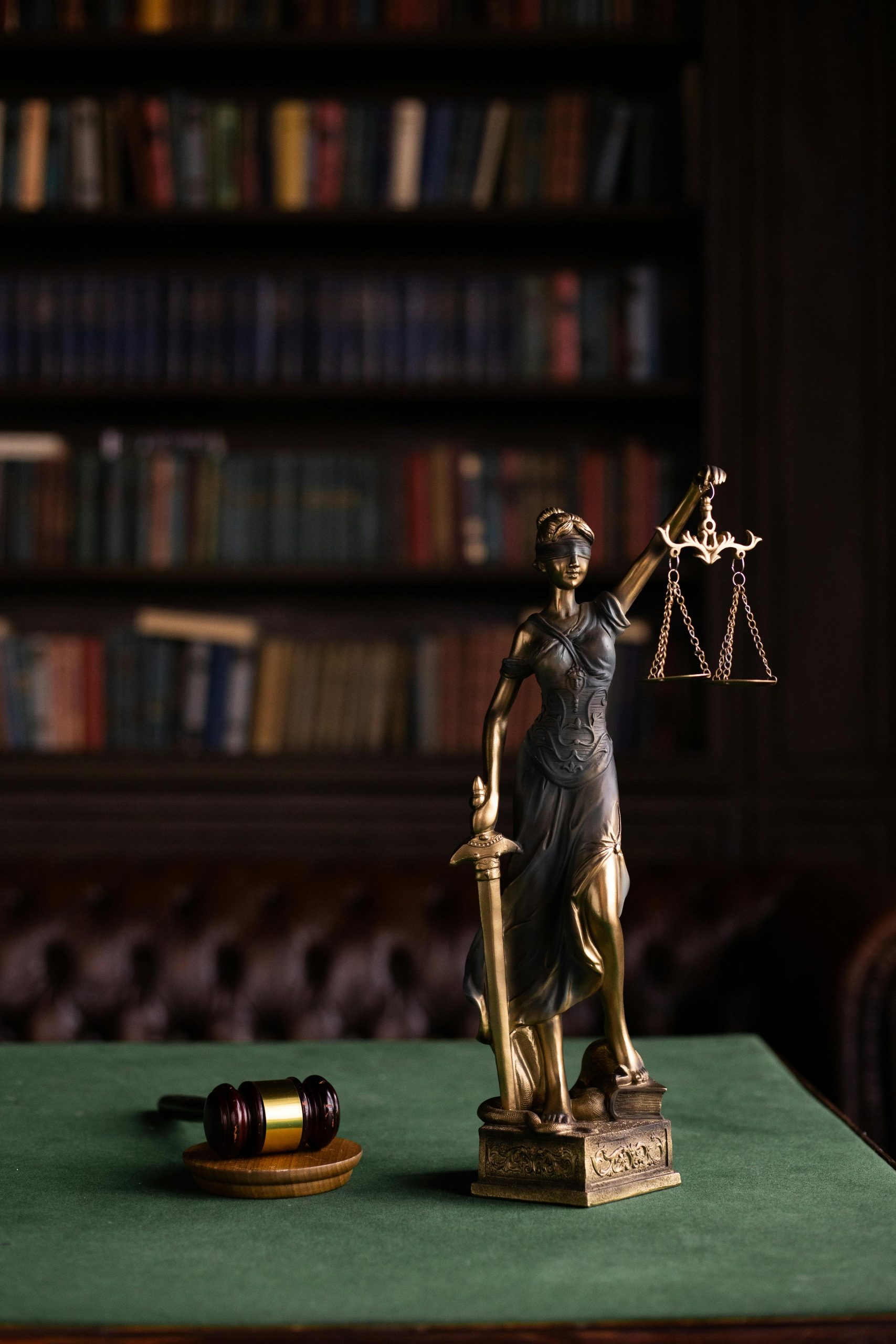
Material handling equipment (MHE) is a critical enabler of operational excellence in businesses across various industries. Efficient and reliable MHE directly impacts productivity, safety, cost-effectiveness, and ultimately, a company’s ability to meet customer demands. The right MHE ensures smooth material flow, optimized warehouse space, and reduced handling times, all contributing to a more streamlined and competitive operation.
Investing in premium MHE offers numerous advantages compared to opting for lower-cost alternatives. Top-tier equipment typically boasts superior durability, advanced technology, enhanced safety features, and lower maintenance costs over its lifespan. While the initial investment may be higher, the long-term benefits of premium MHE often outweigh the upfront costs, leading to greater overall value and a stronger return on investment.
This overview aims to present real-world case studies of companies that have significantly improved their operations by implementing top-tier material handling solutions. By examining these success stories, we will gain valuable insights into the tangible benefits of investing in premium MHE and the strategies employed to achieve operational excellence.
Case Study 1: Automotive Industry – Enhanced Internal Material Handling Management
Company Background and Challenges: A major automotive manufacturer faced significant challenges in its internal material handling operations. Frequent delays in forklift service, high maintenance costs due to an aging fleet, and growing safety concerns were impacting productivity and increasing operational expenses. The internal “customers,” the various departments relying on timely material delivery, expressed dissatisfaction with the current state of affairs.
Solutions Implemented: The company undertook a comprehensive review of its material handling processes and identified key areas for improvement. This included:
- Optimizing forklift routes and dispatch procedures to minimize response times.
- Implementing a more rigorous preventive maintenance program to reduce breakdowns.
- Strategically renting additional forklifts to address peak demand and supplement the existing fleet.
- Investing in operator training to enhance safety and efficiency.
Results: The implemented solutions yielded significant improvements in the company’s internal material handling operations:
- Improved service agility and reliability, resulting in faster material delivery times.
- Reduced costs associated with maintenance and downtime.
- Enhanced overall satisfaction among internal customers due to improved service levels.
Key Takeaways: This case study highlights the importance of regularly evaluating internal customer satisfaction and addressing specific pain points in material flow. By focusing on improving service agility, reliability, and cost-effectiveness, companies can significantly enhance their internal material handling operations and drive overall productivity gains. Addressing the delays in forklift service were solved with changes in material handling.
Case Study 2: Energy Technology Company – Optimized Warehouse and Material Flow
Company Background and Challenges: An energy technology company experienced challenges with inefficient warehouse space utilization, high material handling costs, and suboptimal material flow. These inefficiencies hindered their ability to respond quickly to customer demands and negatively impacted their bottom line.
Solutions Implemented: To address these challenges, the company implemented several key solutions:
- Warehouse Analysis: A comprehensive analysis of the existing warehouse layout, storage strategies, and material flow patterns was conducted to identify areas for improvement.
- Implementation of a Plan for Every Part (PFEP): The company implemented a PFEP to optimize the storage and retrieval of materials, ensuring that the right parts were available at the right time and in the right location.
- Optimized Delivery Routes: Delivery routes within the warehouse were optimized to minimize travel distances and reduce material handling times.
- Transition to More Efficient Delivery Methods: The company transitioned from traditional forklifts to more efficient delivery methods, such as tuggers, to reduce congestion and improve material flow.
Results: The implementation of these solutions resulted in significant improvements in the company’s warehouse operations:
- Improved space utilization, allowing for increased storage capacity within the existing footprint.
- Reduced material handling costs due to more efficient processes and reduced labor requirements.
- Streamlined material flow, resulting in faster order fulfillment and improved customer satisfaction.
Key Takeaways: This case study highlights the benefits of conducting a comprehensive warehouse and material flow analysis to identify inefficiencies and develop targeted solutions. Optimizing delivery routes, implementing a PFEP, and minimizing forklift trips can significantly improve warehouse operations, reduce costs, and enhance overall efficiency.
Case Study 3: Manufacturing – Forklift-Free Operations with Remote Controlled Electric Tugs
Company Background and Challenges: A manufacturer specializing in large-scale heavy plant equipment faced significant material handling challenges within its production facility. The movement of heavy components and assemblies using traditional forklifts posed safety risks, caused congestion, and limited maneuverability in tight spaces.
Solutions Implemented: To address these challenges, the company implemented forklift-free processes by replacing forklifts with remote-controlled electric tugs. These tugs were specifically selected for their ability to safely and efficiently move heavy loads in confined areas.
Results: The transition to remote-controlled electric tugs resulted in:
- Driving safer operations by eliminating the risks associated with forklift operation in congested areas.
- More efficient operations due to improved maneuverability and reduced congestion.
Key Takeaways: This case study demonstrates that remote-controlled electric tugs can provide a safer and more efficient alternative to forklifts in manufacturing environments where handling heavy loads in confined spaces is a challenge.
Case Study 4: Manufacturing – Increased Efficiency with AGV
Company Background: A manufacturing facility sought to optimize its production processes and reduce manual labor in the movement of materials between workstations.
Solutions Implemented: The company implemented Automated Guided Vehicles (AGVs) to automate the transportation of materials throughout the facility.
Results: The implementation of AGVs led to increased efficiency in material handling operations.
Key Takeaways: AGVs can be effectively deployed in manufacturing settings to automate material transport, leading to increased efficiency and reduced reliance on manual labor.
Case Study 5: Coventry Arena – Doubled Efficiency with Bin Mover
Company Background: The Coventry Building Society Arena, a multi-purpose venue and home of Coventry City FC, sought to enhance workplace safety and productivity in moving waste bins. Waste management was labor-intensive, inefficient, and posed a risk of injury to staff.
Solutions Implemented: The arena implemented a MasterMover TOW300 bin towing machine, an electric tug designed to move heavy bins safely and effortlessly. This allowed staff to move two bins simultaneously.
Results: The implementation of the bin mover enabled the arena to double its bin handling efficiency while virtually eliminating the risk of injury. The electric motor takes the strain, enabling staff to move multiple bins with fingertip control.
Key Takeaways: Bin movers can significantly increase efficiency and safety in waste management operations by reducing the physical strain on staff and allowing for the simultaneous movement of multiple bins. This is particularly beneficial in large venues with diverse operational needs.
Conclusion
The case studies presented demonstrate the tangible benefits of investing in premium material handling equipment (MHE) to achieve operational excellence. From enhanced internal material flow in the automotive industry to forklift-free operations in manufacturing, top-tier MHE solutions have enabled companies to improve efficiency, reduce costs, enhance safety, and increase customer satisfaction.
It is crucial to emphasize that there is no one-size-fits-all approach to material handling. The most successful implementations are those that are carefully tailored to address specific operational challenges and align with the unique needs of each business. A thorough assessment of existing processes, identification of bottlenecks, and a clear understanding of desired outcomes are essential for selecting the right MHE solutions.
In conclusion, achieving operational excellence through strategic investments in MHE is not just about acquiring the latest technology; it’s about making informed decisions that optimize material flow, improve productivity, and create a safer and more efficient work environment. By prioritizing quality, reliability, and tailored solutions, businesses can unlock the full potential of their material handling operations and achieve a sustainable competitive advantage.