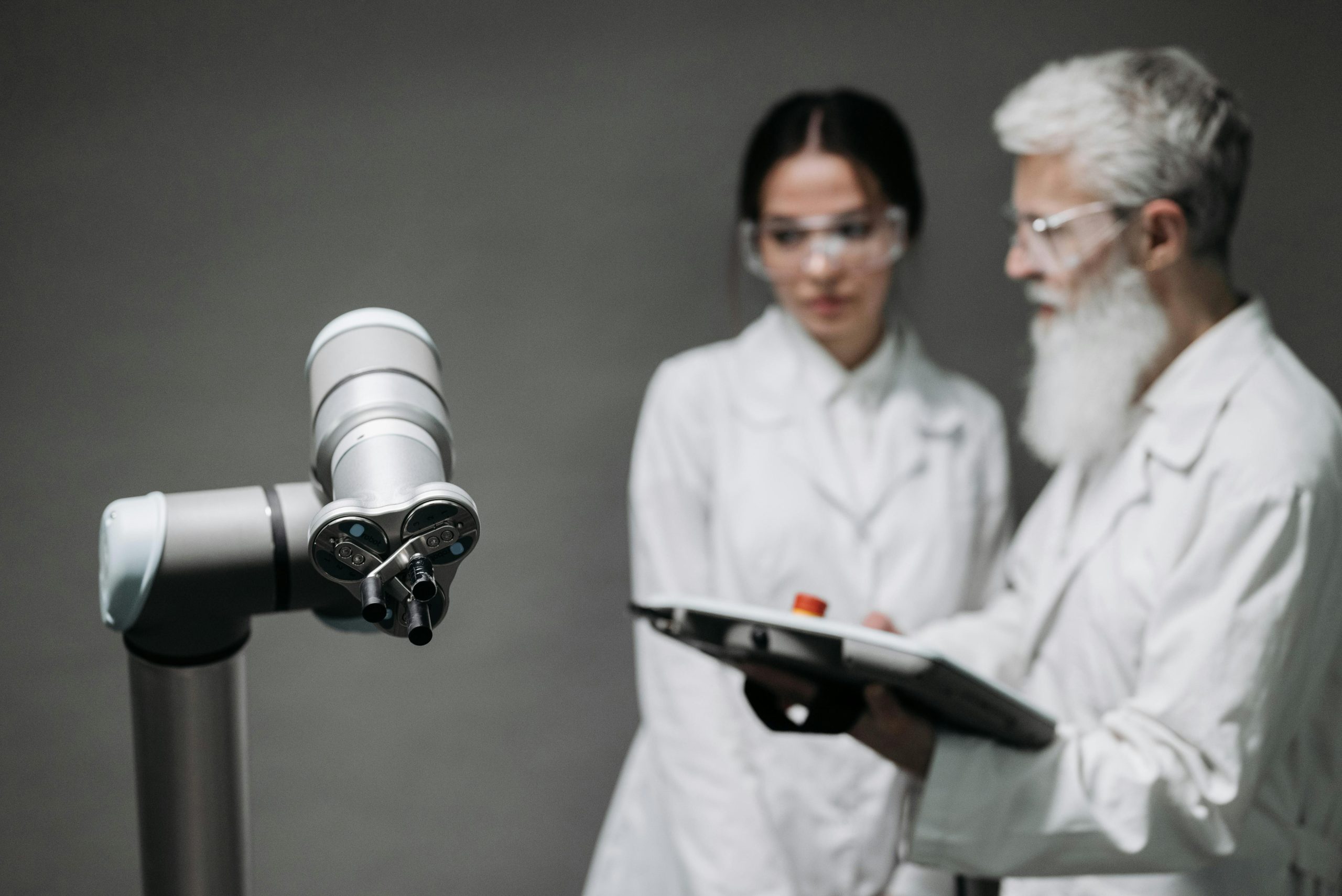
The material handling industry is a critical component of global commerce, encompassing the movement, storage, control, and protection of materials and products throughout the supply chain. From manufacturing and distribution to warehousing and transportation, efficient material handling is essential for optimizing operations, reducing costs, and ensuring timely delivery of goods to consumers.
In today’s increasingly competitive and demanding marketplace, there is a growing need for high-quality, efficient material handling equipment (MHE). Businesses are seeking solutions that can enhance productivity, improve safety, reduce labor costs, and minimize environmental impact. This has fueled a wave of technological innovation, transforming the MHE landscape and paving the way for a smarter, more efficient future.
This overview aims to explore the latest technological innovations driving the future of high-quality material handling equipment. From automation and robotics to IoT and advanced sensor technologies, we will delve into the cutting-edge solutions that are revolutionizing the industry and enabling businesses to achieve unprecedented levels of efficiency and performance.
Automation and Robotics Integration
Automation plays a pivotal role in enhancing efficiency and reducing labor costs within the material handling industry. By automating repetitive and physically demanding tasks, businesses can optimize their operations, improve productivity, and free up human workers to focus on more complex and strategic activities. The integration of robotics is at the forefront of this automation revolution.
- Automated Guided Vehicles (AGVs) and Autonomous Mobile Robots (AMRs): These vehicles offer flexible navigation, enhanced safety features, and the ability to operate continuously without human intervention. AGVs typically follow predefined paths using wires, magnetic strips, or lasers, while AMRs utilize advanced sensors and software to navigate autonomously, adapting to changing environments.
- Collaborative Robots (Cobots): Cobots are designed to work alongside human workers in a safe and collaborative manner. They excel at precise manipulation tasks, offering adaptability and quick reprogramming capabilities to handle a variety of material handling tasks.
- Robotic Systems: Robotic systems are increasingly being used in material handling for tasks such as picking, packing, and palletizing. These systems can significantly increase throughput, reduce errors, and improve overall efficiency in these critical processes.
- AI and Machine Learning: Artificial intelligence (AI) and machine learning (ML) are transforming material handling by enabling predictive maintenance and real-time optimization. Proper AI data labeling is necessary for the training of AI models to identify patterns and make smart decisions in material handling that can improve the overall performance of a system. AI-powered systems can analyze data from sensors and other sources to predict equipment failures, optimize routes, and improve overall system performance.
Through the integration of automation and robotics, businesses can achieve significant gains in efficiency, productivity, and safety, paving the way for a more streamlined and cost-effective material handling operation.
Innovations in Picking Technologies
Innovations in picking technologies are revolutionizing order fulfillment and warehouse operations, streamlining the process and increasing efficiency. Next-generation robotic systems are at the forefront of this transformation, offering advanced capabilities that surpass traditional manual picking methods.
Key advancements in picking technologies include:
- Next-Generation Robotic Systems: These systems are designed to automate the picking process, reducing the need for manual labor and increasing throughput.
- Advanced Machine Learning Algorithms: Machine learning algorithms enable robots to learn from experience, improving their picking accuracy and efficiency over time.
- Precision Gripping Mechanisms: Advanced gripping mechanisms allow robots to handle a wide variety of products with varying shapes, sizes, and textures, ensuring gentle and secure handling.
- 3D Vision Systems and Adaptive Learning Capabilities: 3D vision systems provide robots with a detailed understanding of their environment, allowing them to accurately identify and locate items for picking. Adaptive learning capabilities enable robots to adjust their picking strategies based on real-time feedback, optimizing their performance for different tasks.
IoT and Smart Sensors
The Internet of Things (IoT) plays a crucial role in enhancing tracking and monitoring within material handling operations. By connecting devices and systems through a network, IoT enables real-time visibility, improved decision-making, and optimized processes.
- RFID and Smart Sensing: Radio-Frequency Identification (RFID) and other smart sensing technologies are used for real-time inventory monitoring and optimized warehouse utilization. RFID tags attached to items transmit data to readers, providing instant updates on location and status without needing a line of sight. This automated tracking improves inventory accuracy, reduces errors, and increases operational speed.
- Machine Vision: Machine vision systems enhance quality control and defect detection by automatically inspecting products and identifying any deviations from pre-defined standards.
- Real-time Data: IoT sensors provide real-time data on the condition and location of goods, enabling businesses to have a clear picture of their inventory levels at any given time. This eliminates the need for manual counts or guesswork, allowing for informed decisions and preventing stockouts or overstocking.
- Optimizing Routes: The data collected by IoT sensors is used to optimize routes and ensure efficient material handling. By tracking the movement of goods in real-time, businesses can identify bottlenecks, streamline workflows, and improve overall productivity.
With IoT and smart sensors, businesses can achieve full inventory visibility, improve accuracy, and optimize their material handling processes, resulting in increased efficiency and reduced costs.
Advancements in Forklift Technologies
Forklift technology is continually evolving, driven by the need for greater efficiency, safety, and sustainability. Recent advancements are transforming these essential material handling vehicles into smarter, more reliable, and environmentally friendly machines.
- Lithium-ion Powered Forklifts: Lithium-ion batteries are replacing traditional lead-acid batteries in forklifts, offering significant advantages such as improved energy efficiency, faster recharging times, and reduced maintenance requirements.
- Operator Assistance Systems: These systems enhance safety and productivity by providing operators with real-time feedback and assistance. Features include proximity sensors to prevent collisions, hydraulic function control to ensure smooth and precise movements, and dynamic operator alerts to warn of potential hazards.
- Forklift Tire Technology: Innovations in forklift tire technology include tread-wear indicators to monitor tire condition and optimized grip patterns to improve traction and stability.
- Sensors: Sensors are being integrated into forklifts to improve performance and efficiency. These sensors can monitor load weight, detect obstacles, and optimize fuel consumption.
Conveyor Belt Innovations
Conveyor belts are a fundamental component of many material handling systems, and ongoing innovations are enhancing their performance and versatility. Advanced conveyor systems are being developed for specialized applications, particularly in industries like food processing, where hygiene and sanitation are paramount.
- Advanced Conveyor Systems for Food Processing and Other Industries: These systems incorporate features such as easy-to-clean surfaces, corrosion-resistant materials, and modular designs to meet the stringent requirements of food processing and other industries.
- Metal Belts with Increased Open Area to Reduce Material Build-Up: Metal conveyor belts with increased open area are designed to minimize material build-up, preventing contamination and simplifying cleaning. This is particularly important in applications where sticky or wet materials are being conveyed.
Augmented Reality (AR)
Augmented Reality (AR) is emerging as a valuable tool in material handling, offering innovative solutions for training and operational efficiency. By overlaying digital information onto the real world, AR enhances the user experience and provides valuable guidance to operators.
- Enhanced Training: AR can be used to provide interactive and immersive training experiences for operators. Trainees can use AR headsets or mobile devices to visualize equipment operation, practice maintenance procedures, and learn safety protocols in a safe and controlled environment. AR can also provide real-time guidance for tasks, such as equipment repair or order picking, overlaying instructions and visual cues onto the operator’s field of view.
- Error Reduction: AR helps in reducing errors and increasing operational efficiency. By providing real-time information and guidance, AR can assist operators in making informed decisions and completing tasks accurately. For example, AR can be used to verify the correct item is being picked for an order, reducing the risk of errors and improving order fulfillment accuracy.
Drones and UAVs (Unmanned Aerial Vehicles)
Drones, also known as Unmanned Aerial Vehicles (UAVs), are emerging as a transformative technology in material handling, poised to revolutionize operations, particularly in large warehouses and distribution centers.
- Airborne Solutions: Drones offer a unique aerial perspective, enabling them to access areas that are difficult or dangerous for humans to reach. This makes them well-suited for tasks such as inspecting high shelves, monitoring inventory levels, and conducting safety checks in large, sprawling warehouses.
- Quick Inventory: Drones can conduct rapid inventory checks by scanning barcodes or RFID tags from the air, providing real-time updates on stock levels and locations. This eliminates the need for manual inventory counts, saving time and reducing errors.
Conclusion
In summary, the material handling industry is undergoing a significant transformation driven by a wave of technological innovations. From automation and robotics to IoT and augmented reality, these advancements are enabling businesses to achieve unprecedented levels of efficiency, safety, and sustainability in their operations.
Adopting these technologies is crucial for businesses seeking to enhance their efficiency and maintain uncompromised quality in today’s competitive marketplace. By embracing automation, integrating smart sensors, and leveraging data analytics, companies can optimize their material handling processes, reduce costs, and improve customer satisfaction.
Looking ahead, the future of material handling will be shaped by further advancements in artificial intelligence, machine learning, and robotics. As these technologies continue to evolve, they will unlock new opportunities for businesses to streamline their operations, improve decision-making, and create more resilient and agile supply chains. The impact of these innovations will be felt across various industries, transforming the way materials are moved, stored, and managed, and paving the way for a more efficient and sustainable future.